Safarir
(Charles)
Today's project was to repair the busted lead screw support for my Graziano. I forgot to take a picture of the part in it original condition but it is quite easy to imagine. I started by grinding away the broken cast iron with a rotary burr and strip some of the paint with some roloc paint stripping pad. I use those on my M12 Die Grinder and they work amazingly well.
I never braze before and to be honest, I just got my oxy-acetylene torch about 1 week ago and bought brazing rod at princess auto this morning. After some experimentation with some test piece, I felt ready for it and went for it. I made sure to slowly pre-heat the part as much as possible to prevent building to much stress in the part.
Not pretty, but also not as bad as I expected. I covered the part in welding blanket to let it cool slowly. One thing I really learned for next time: Just remove all the paint on the part:
Here it is after a quick trip on the milling machine
I am not too concern about the porosity, but after looking at it correctly, I did not feel I had enough material to fix the bore correctly. So after stripping the paint completely, here we go for round 2.
For some reason, the second pass felt even more difficult. When trying to work inside the bore, I had my torch die on me a couple of time. I think my acetylene pressure was too low. Here it is after a quick pass on the milling.
There is still quite a bit of porosity, but at least I seem to have plenty of material to fix this bore correctly. Next step, chuck this in the 4 jaws...
Oups ... it doesn't fit ... My 8" chuck is a tiny bit too small for the part.
The next logical solution is to throw this on the mill and bore it with a boring head, but I am still waiting for the right boring head to pop up at auction... I am now tempted to simply buy a chinese one, but don't really want to wait for one. Anyone have a good lead on a decent boring head ?
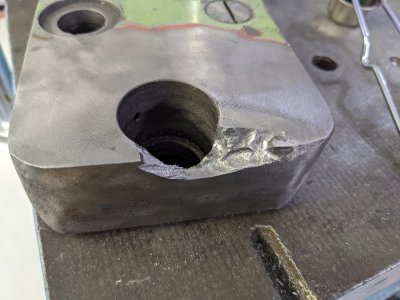
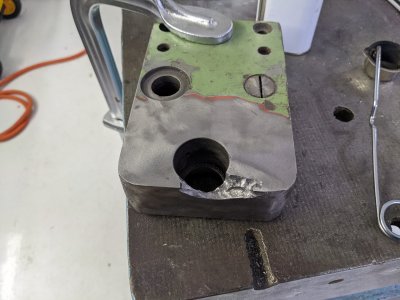
I never braze before and to be honest, I just got my oxy-acetylene torch about 1 week ago and bought brazing rod at princess auto this morning. After some experimentation with some test piece, I felt ready for it and went for it. I made sure to slowly pre-heat the part as much as possible to prevent building to much stress in the part.
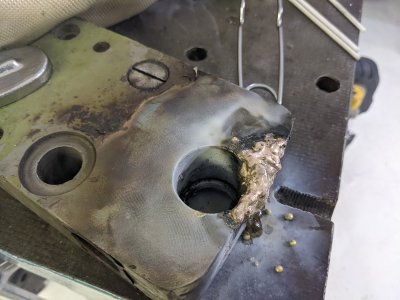
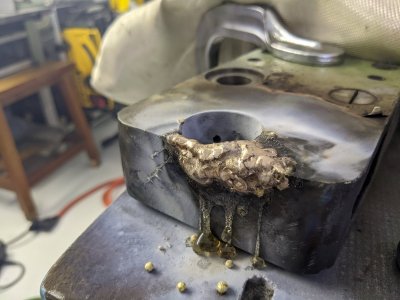
Not pretty, but also not as bad as I expected. I covered the part in welding blanket to let it cool slowly. One thing I really learned for next time: Just remove all the paint on the part:
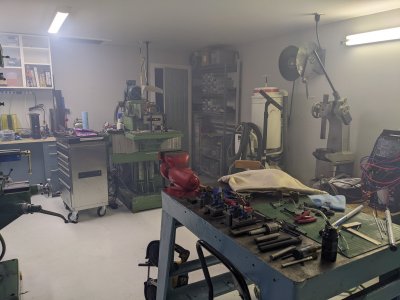
Here it is after a quick trip on the milling machine
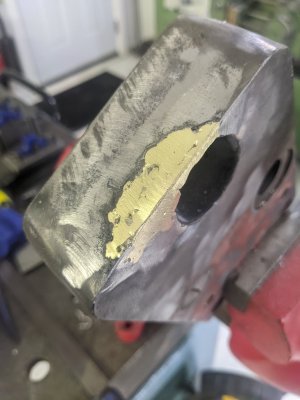
I am not too concern about the porosity, but after looking at it correctly, I did not feel I had enough material to fix the bore correctly. So after stripping the paint completely, here we go for round 2.
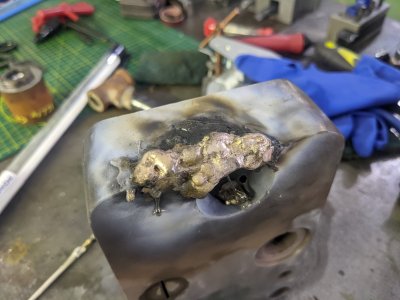
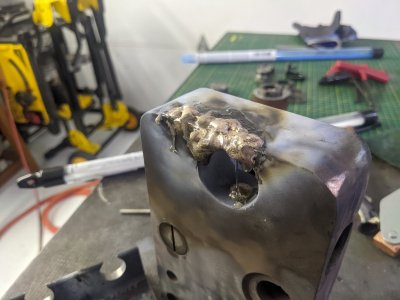
For some reason, the second pass felt even more difficult. When trying to work inside the bore, I had my torch die on me a couple of time. I think my acetylene pressure was too low. Here it is after a quick pass on the milling.

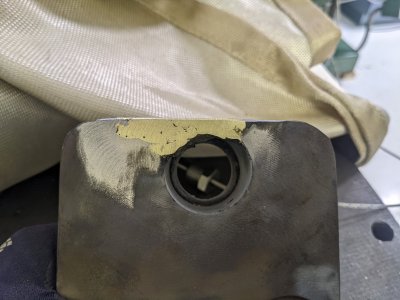
There is still quite a bit of porosity, but at least I seem to have plenty of material to fix this bore correctly. Next step, chuck this in the 4 jaws...
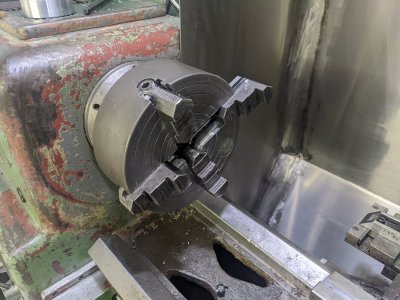
Oups ... it doesn't fit ... My 8" chuck is a tiny bit too small for the part.
The next logical solution is to throw this on the mill and bore it with a boring head, but I am still waiting for the right boring head to pop up at auction... I am now tempted to simply buy a chinese one, but don't really want to wait for one. Anyone have a good lead on a decent boring head ?