trlvn
Ultra Member
I've got a little project and I think maybe a bearing-bronze bushing is the right answer but I'd like some input.
Background: I bought a tiny table saw--a model maker's saw with a 4 inch blade. It is old and the blade arbor (9/16 in. diameter) has a noticeable amount of play or slop. It is just a steel shaft running in cast iron 'pillow' and the hole has enlarged and become egg shaped. There is a hole in the casting for oiling but it doesn't look like it was regularly lubricated...if at all!
BTW, I believe the arbor needs to turn pretty fast because of the small diameter blade. Maybe 6,000 to 9,000 rpm. I also need a motor to drive this thing but that is a separate problem. I might well try to power it with a corded Dremel tool.
I think I want to bore or ream out the casting and press in a bronze sleeve bearing. I will polish the shaft a bit which should give a few thous of clearance in the bearing. None of this is really ultra high precision--the saw was originally pretty cheaply made. However, given the shaft rpm, I think it deserves a reasonable bearing surface. The outer diameter of the casting is about 1.05 inches so I don't have a lot of 'meat' to work with.
An alternative might be to enlarge and plug the existing hole with a small chunk of cast iron and bore a new hole. Obviously, it survived for years with the steel shaft running in cast iron.
Any thoughts on a good approach?
If I go with a bronze sleeve, what are some good suppliers to look at? I would need 9/16 ID, OD could be 11/16 or 3/4 and length would be close to 2 inches. My local bearing supply place (Ted's Bearing, Oakville) does not have anything close.
Thanks for any input.
Craig
PS I couldn't resist this saw; super cute. Got it for $5 in an auction!!
Background: I bought a tiny table saw--a model maker's saw with a 4 inch blade. It is old and the blade arbor (9/16 in. diameter) has a noticeable amount of play or slop. It is just a steel shaft running in cast iron 'pillow' and the hole has enlarged and become egg shaped. There is a hole in the casting for oiling but it doesn't look like it was regularly lubricated...if at all!
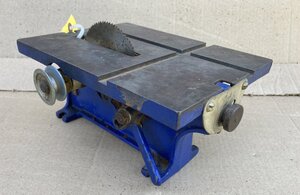
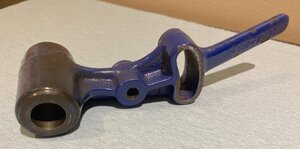
BTW, I believe the arbor needs to turn pretty fast because of the small diameter blade. Maybe 6,000 to 9,000 rpm. I also need a motor to drive this thing but that is a separate problem. I might well try to power it with a corded Dremel tool.
I think I want to bore or ream out the casting and press in a bronze sleeve bearing. I will polish the shaft a bit which should give a few thous of clearance in the bearing. None of this is really ultra high precision--the saw was originally pretty cheaply made. However, given the shaft rpm, I think it deserves a reasonable bearing surface. The outer diameter of the casting is about 1.05 inches so I don't have a lot of 'meat' to work with.
An alternative might be to enlarge and plug the existing hole with a small chunk of cast iron and bore a new hole. Obviously, it survived for years with the steel shaft running in cast iron.
Any thoughts on a good approach?
If I go with a bronze sleeve, what are some good suppliers to look at? I would need 9/16 ID, OD could be 11/16 or 3/4 and length would be close to 2 inches. My local bearing supply place (Ted's Bearing, Oakville) does not have anything close.
Thanks for any input.
Craig
PS I couldn't resist this saw; super cute. Got it for $5 in an auction!!