140mower
Don
I'm pretty sure that I have shown the collet chuck I made for my South Bend 10k, well over the weekend I was talking to @JustaDB on the phone and mentioned that a collet chuck would be a great project for his new to him 9a. I dug through the pictures on this phone and realized that I was over half finished the thing when I got this phone. (I had a sad go of it in that time period where two phones committed suicide in a short period of time. Both jumped to their demise, probably took too many selfies for their liking.) Alas, some pictures are recreations, so if something doesn't seem right, it might not be.... If anyone has any ideas or sees a better way, jump in and let's see if we can get James into a little project. 
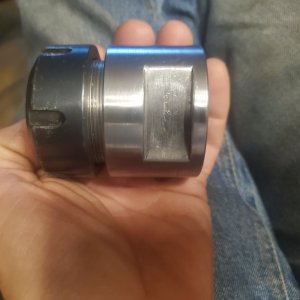