eotrfish
Super User
I make some fly reels which have a shallow (4Deg to 8Deg) taper on the flanges. I try for a mirror finish without having to polish after the parts come off the lathe. Turning the compound by hand without leaving any tooling marks is a PITA.
I found a couple of small 27V DC gear motors in my collection of "useful someday stuff" - always good to have backup
The whole assembly is secured to the top of the compound with 4 8-32 socket head caps.
Since the motor is DC it can be reversed. Although the motor is rated at 27VDC I've run it from 12VDC to 40VDC. All the voltage change does is change the compound feed rate. So far 27VDC seems just right for a near mirror finish.
The idler gear train pivots on the motor centerline to engage or disengage the gear mounted on the compound handwheel - effectively turning the compound feed on or off.
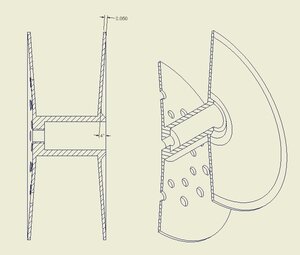
I found a couple of small 27V DC gear motors in my collection of "useful someday stuff" - always good to have backup
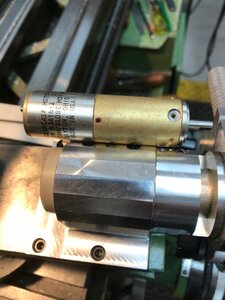
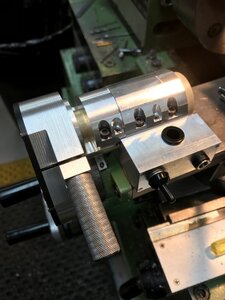
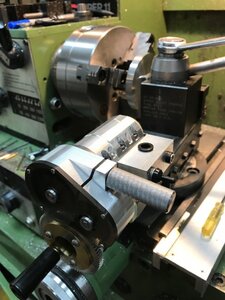
The whole assembly is secured to the top of the compound with 4 8-32 socket head caps.
Since the motor is DC it can be reversed. Although the motor is rated at 27VDC I've run it from 12VDC to 40VDC. All the voltage change does is change the compound feed rate. So far 27VDC seems just right for a near mirror finish.
The idler gear train pivots on the motor centerline to engage or disengage the gear mounted on the compound handwheel - effectively turning the compound feed on or off.
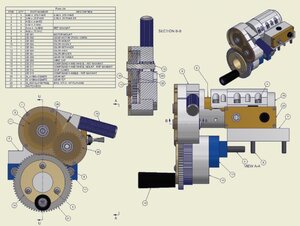