SomeGuy
Hobbyist
For my RC build I am going to be making some sprocket mounts for fitting to a shaft. Here's what one of the sprockets look like:
So I need to make a small mount with at least 4 bolt holes that will line up with the holes in the sprocket but I don't have a mill (yet). I do have a drill press though.
I was thinking I could just make a simple jig where I use one of the sprockets as a template to put a pin on a scrap steel plate for the center and drill 4 holes, tap them (so I can securely pin the parts in place), then use the template to locate the holes on the sprocket mount and ensure spacing while drilling on the drill press.
Needs to be fairly accurate as these will be spinning at upwards of ~2000rpm, material will be aluminum.
Any better ideas?
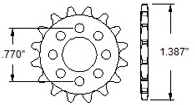
So I need to make a small mount with at least 4 bolt holes that will line up with the holes in the sprocket but I don't have a mill (yet). I do have a drill press though.
I was thinking I could just make a simple jig where I use one of the sprockets as a template to put a pin on a scrap steel plate for the center and drill 4 holes, tap them (so I can securely pin the parts in place), then use the template to locate the holes on the sprocket mount and ensure spacing while drilling on the drill press.
Needs to be fairly accurate as these will be spinning at upwards of ~2000rpm, material will be aluminum.
Any better ideas?