We’ve all been there: work on something seemingly unrelated and then realize that, wait a minute, woulden’t it be great to use this machine for that task.
Well, I am designing and figuring out a way to make a gap piece for my CMT Ursus 250 that is missing. I am making it up in wood right now. I’ll post the thoughts, design ideas and manufacture of it on the CMT Ursus lathe series thread.
So I thought why not use the FP3 mill to make the gap piece? Good idea, except it has this ”funny” noise when it runs. So I started digging into it a bit, and promptly opened a big can of worms…
The input shaft pulley is worn very badly. The key is chowdered up. The 25mm shaft has a worn spot. The manual hand wheel to rotate the input shaft for ease of gear changes is missing and with it the retaining plate to hold the pulley onto the shaft.
I’ll take a picture of the shaft once I get it out of the machine…
Which brings me to the next problem: there is a thrust washer that was induction welded onto the input shaft at assembly. It is used to provide a means to set the bearing pre-load of the nested, larger, secondary shaft which is coaxial with the long input shaft which runs through it. The thrust bearing is item 2001 452 in the diagram below.
Here is the parts diagram showing the assembly.
There are three supports for the two shafts: one on each end of the gearbox and one on the central bulkhead. The input shaft is the lower of the two shafts in this picture. It runs all the way through the bigger shaft on the right with the bull gear and the other 4 gears to its right.
And here is the welded thrust washer
The way this needs to come apart is for the long input shaft to slide out the left side as viewed from the access panel. The cluster gear (2001 30 416) will slide on the splines and remain inside the gearbox as the shaft moves left. However, the welded washer (2001 558) will not allow the gear set to slide off the right side. Anything to the right of that washer (2001 31 414) is part of the nested secondary shaft and would remain inside the gearbox as the smaller input shaft is pulled out through its bore.
So, I need to (most likely) destroy the welded washer, grind the splines sufficiently to allow the cluster gear to slide off, and pull the shaft out. I will get all the dimensions I can off the washer before destruction. I’ll need to make a new one for re-assembly. Not sure why it was so important to weld it to the shaft in the first place as it sits hard against the shoulder created by the splines to its left. Perhaps there is an anti rotation requirement? I won’t have a way to weld it in place. I may look into making some sort of key for it.
Before I start destroying the washer, I’ll revisit the whole thing again to make sure I have not missed another solution.
Have any of you come across a similar situation? What did you do? I am wide open to suggestions on this one.
Well, I am designing and figuring out a way to make a gap piece for my CMT Ursus 250 that is missing. I am making it up in wood right now. I’ll post the thoughts, design ideas and manufacture of it on the CMT Ursus lathe series thread.
So I thought why not use the FP3 mill to make the gap piece? Good idea, except it has this ”funny” noise when it runs. So I started digging into it a bit, and promptly opened a big can of worms…
The input shaft pulley is worn very badly. The key is chowdered up. The 25mm shaft has a worn spot. The manual hand wheel to rotate the input shaft for ease of gear changes is missing and with it the retaining plate to hold the pulley onto the shaft.
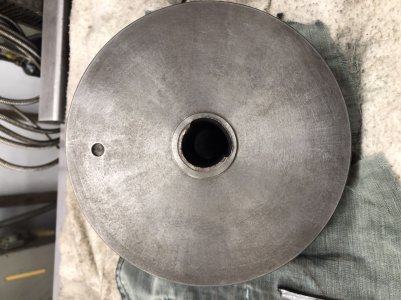
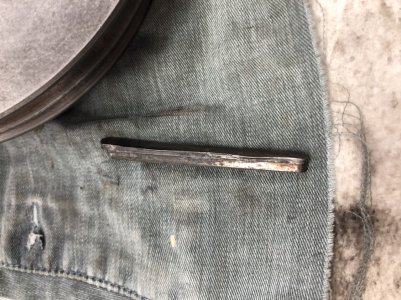
I’ll take a picture of the shaft once I get it out of the machine…
Which brings me to the next problem: there is a thrust washer that was induction welded onto the input shaft at assembly. It is used to provide a means to set the bearing pre-load of the nested, larger, secondary shaft which is coaxial with the long input shaft which runs through it. The thrust bearing is item 2001 452 in the diagram below.
Here is the parts diagram showing the assembly.
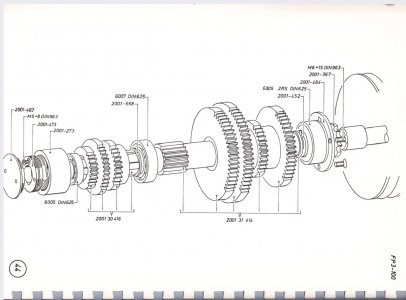
There are three supports for the two shafts: one on each end of the gearbox and one on the central bulkhead. The input shaft is the lower of the two shafts in this picture. It runs all the way through the bigger shaft on the right with the bull gear and the other 4 gears to its right.
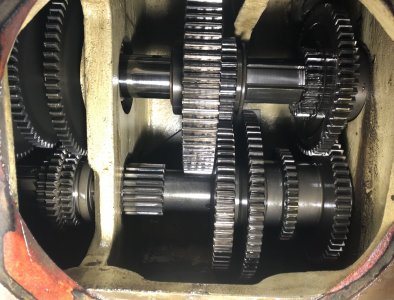
And here is the welded thrust washer
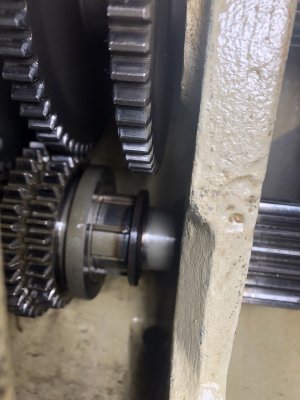
The way this needs to come apart is for the long input shaft to slide out the left side as viewed from the access panel. The cluster gear (2001 30 416) will slide on the splines and remain inside the gearbox as the shaft moves left. However, the welded washer (2001 558) will not allow the gear set to slide off the right side. Anything to the right of that washer (2001 31 414) is part of the nested secondary shaft and would remain inside the gearbox as the smaller input shaft is pulled out through its bore.
So, I need to (most likely) destroy the welded washer, grind the splines sufficiently to allow the cluster gear to slide off, and pull the shaft out. I will get all the dimensions I can off the washer before destruction. I’ll need to make a new one for re-assembly. Not sure why it was so important to weld it to the shaft in the first place as it sits hard against the shoulder created by the splines to its left. Perhaps there is an anti rotation requirement? I won’t have a way to weld it in place. I may look into making some sort of key for it.
Before I start destroying the washer, I’ll revisit the whole thing again to make sure I have not missed another solution.
Have any of you come across a similar situation? What did you do? I am wide open to suggestions on this one.