terry_g
Ultra Member
I picked up a couple insert type threading bars a left and a right. They are decent quality for the price.
Rather than thread toward a shoulder I usually thread with the lathe in reverse and the tool bit upside down.
With the treading bar I was able to cut threads with the cutter on the back side of the stock right side up.
I like to watch the chips coming off as the threads cut.
This was practice cutting 5/8" 18 threads on a piece of mystery metal. I fed the bit in straight next time I will
try cutting with the compound set to 29 degrees.
Rather than thread toward a shoulder I usually thread with the lathe in reverse and the tool bit upside down.
With the treading bar I was able to cut threads with the cutter on the back side of the stock right side up.
I like to watch the chips coming off as the threads cut.
This was practice cutting 5/8" 18 threads on a piece of mystery metal. I fed the bit in straight next time I will
try cutting with the compound set to 29 degrees.
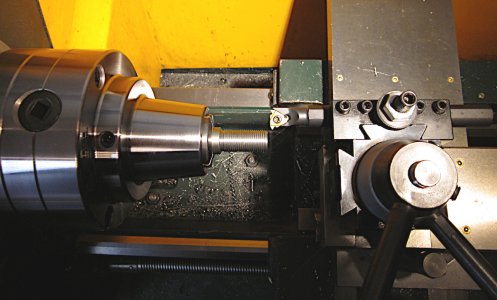