I don't know anyone who likes changing belts positions to change speed on a drill press. I cursed many times after drilling a 1/8" pilot hole then having to change belts positions for a 1/2" drill bit to finish the hole. I've had this project in mind for a while now and finally found great deal on a 1.5 HP three phase motor (thanks Chad).I bought an inexpensive 1.5KW (2 HP) vfd on Amazon as well as an electrical box to house it.
I made up a bracket from some 3/16" aluminum to hold the vfd, control panel and tachometer. I cut the rectangular holes for the panel and tach on the mill before I riveted the bracket parts together.
I removed the top belt housing along with the spindle, idler and motor pulleys. I used an automotive a/c compressor clutch puller to remove the motor and spindle pulleys. I had to machine a couple of pusher slugs to work with the puller.
I mounted the tach magnet with epoxy to the bottom of the spindle pulley after milling a shallow pocket for it. I drilled a hole to mount the pick-up in the bottom of the belt shroud to align the pick-up with the magnet.
e.
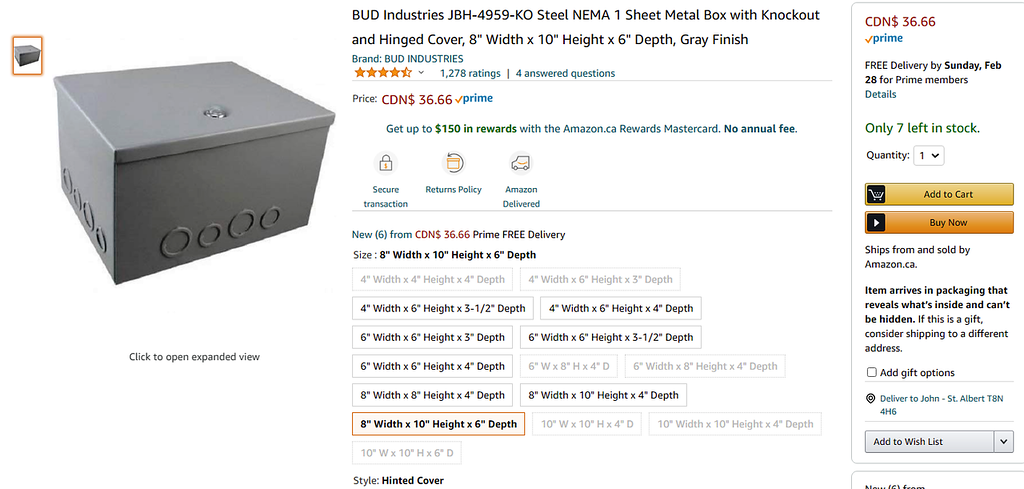
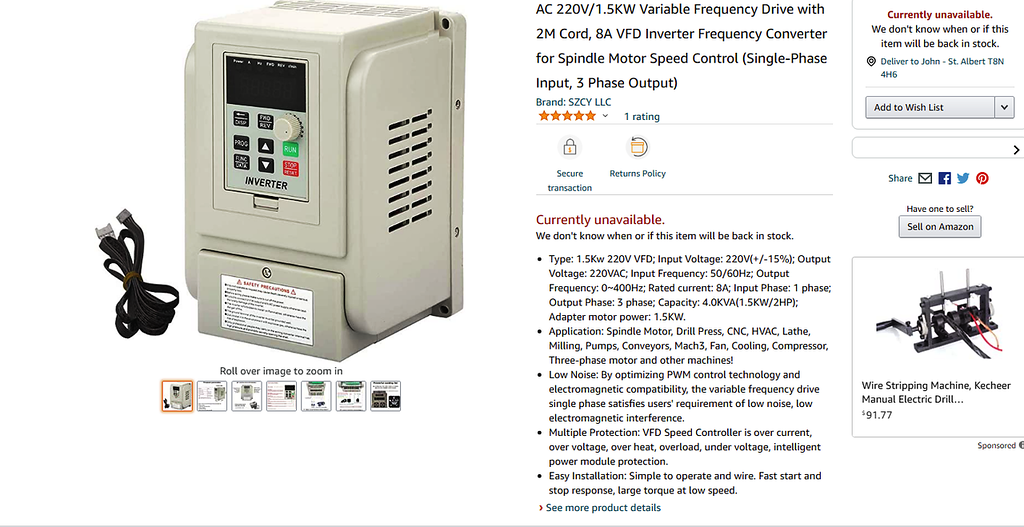
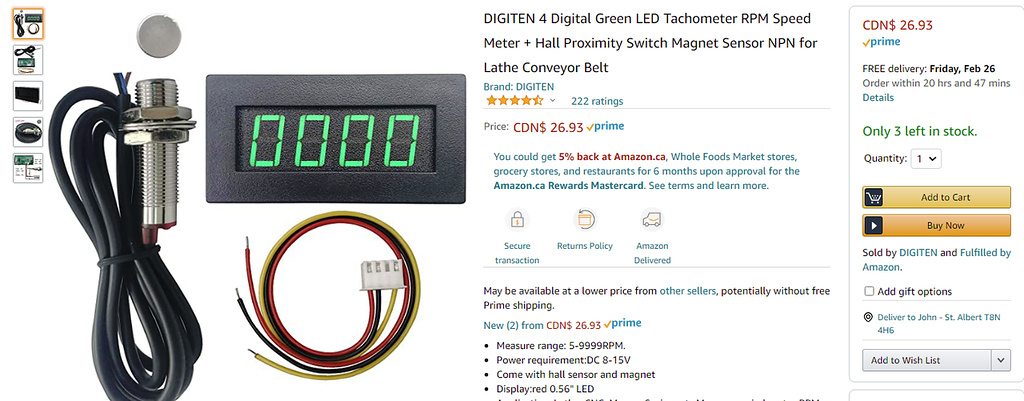
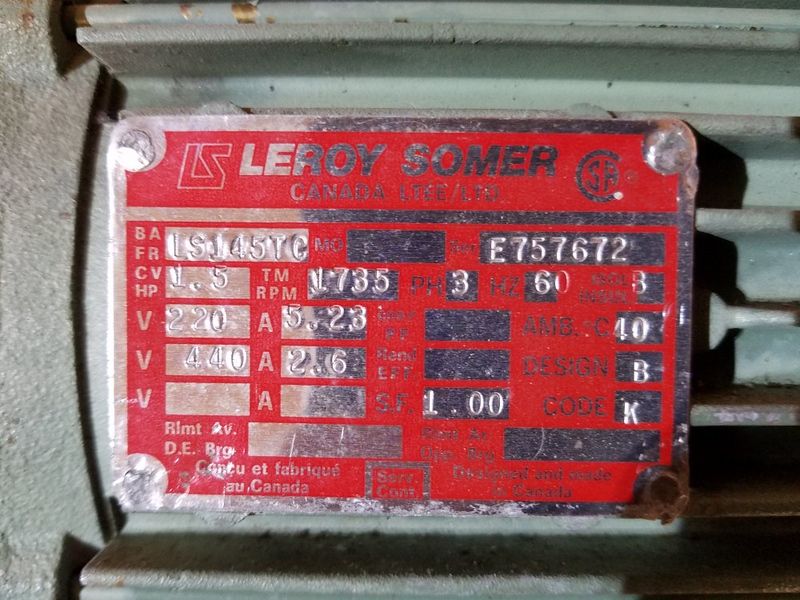
I made up a bracket from some 3/16" aluminum to hold the vfd, control panel and tachometer. I cut the rectangular holes for the panel and tach on the mill before I riveted the bracket parts together.
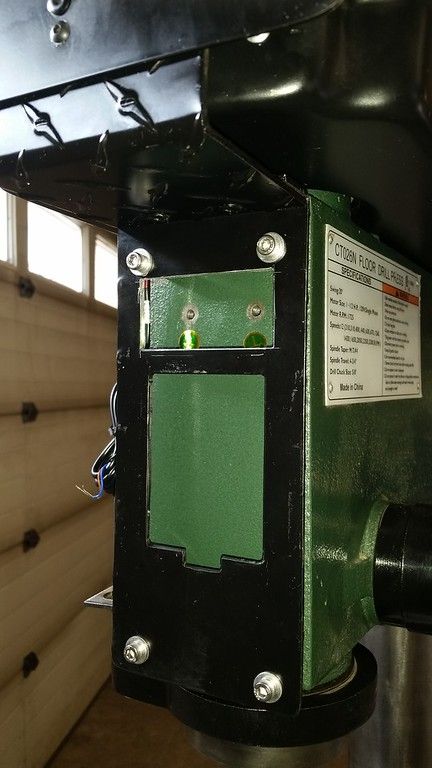
I removed the top belt housing along with the spindle, idler and motor pulleys. I used an automotive a/c compressor clutch puller to remove the motor and spindle pulleys. I had to machine a couple of pusher slugs to work with the puller.
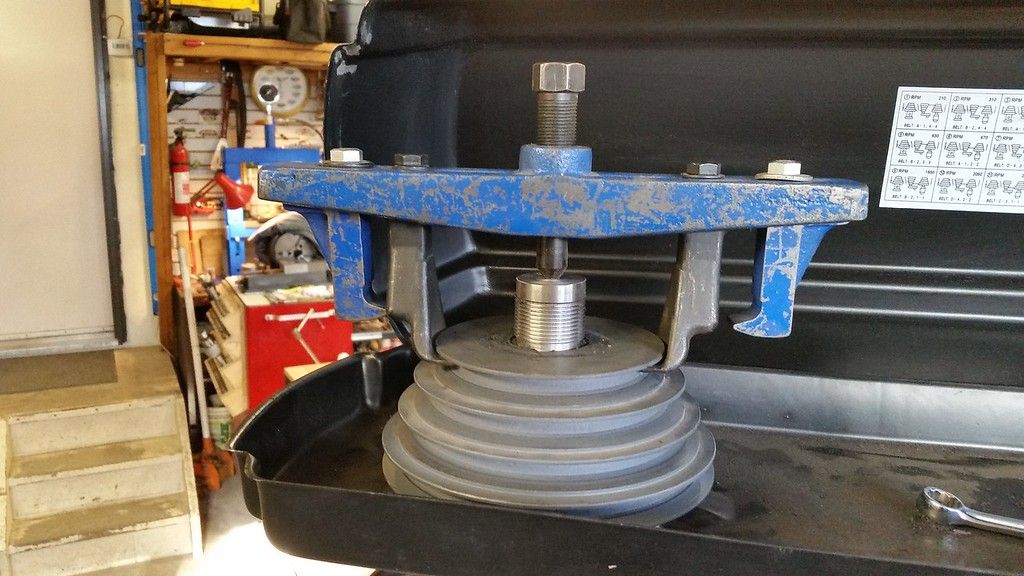
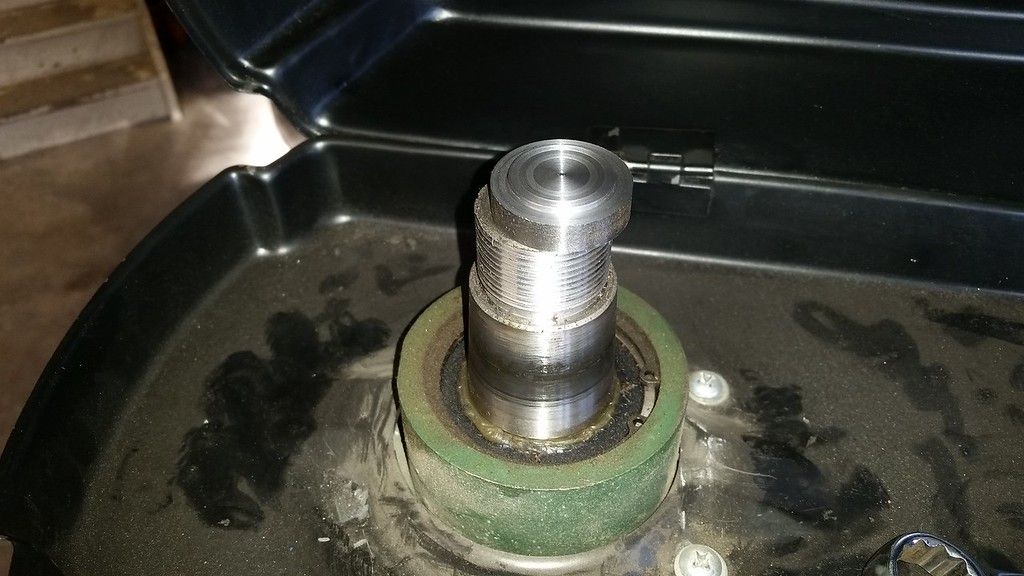
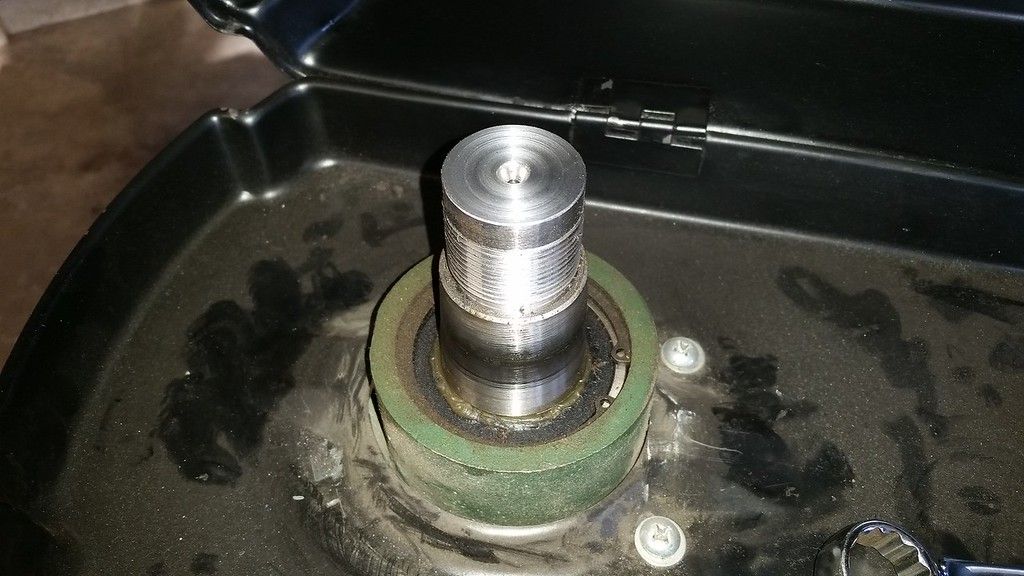
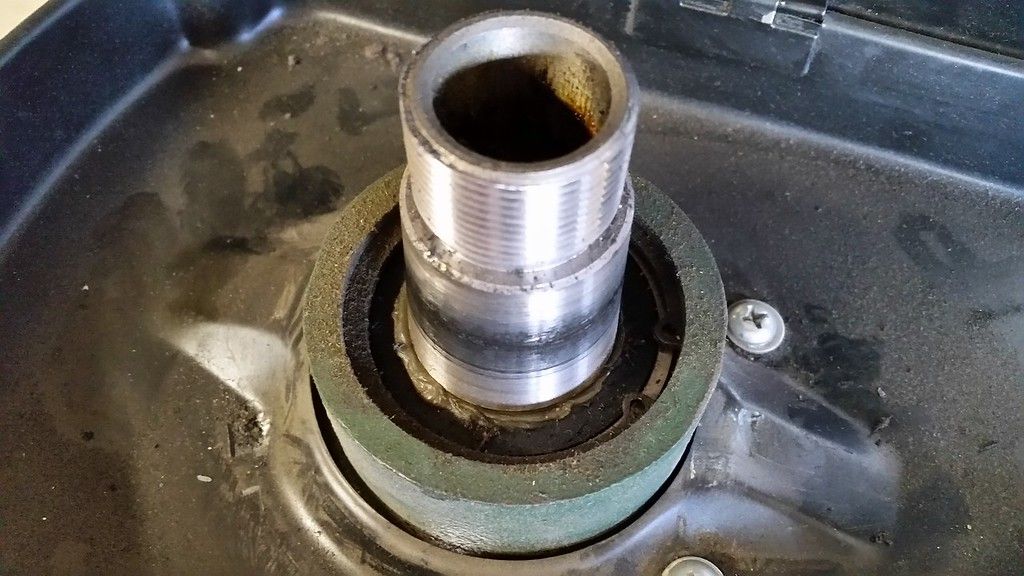
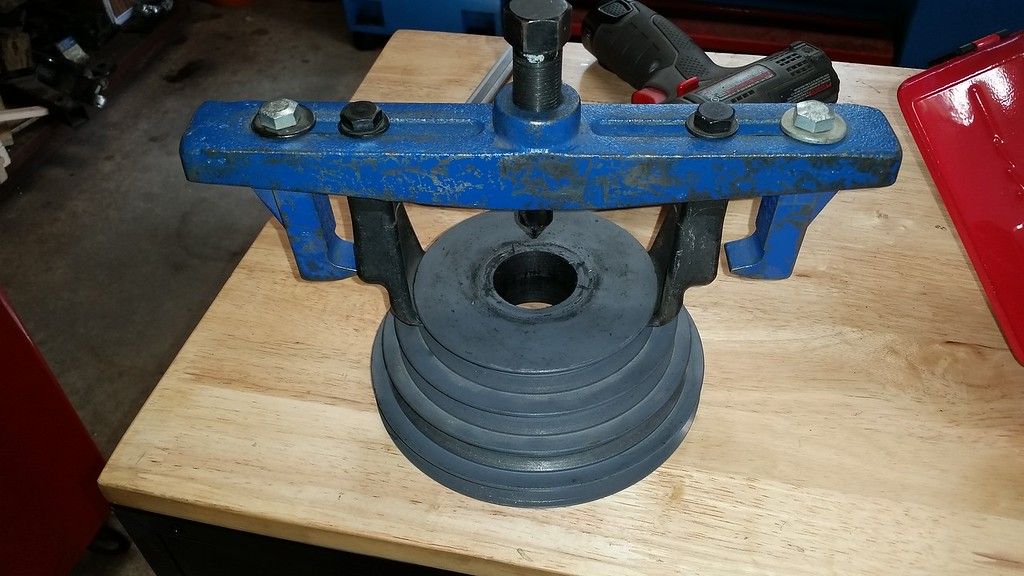
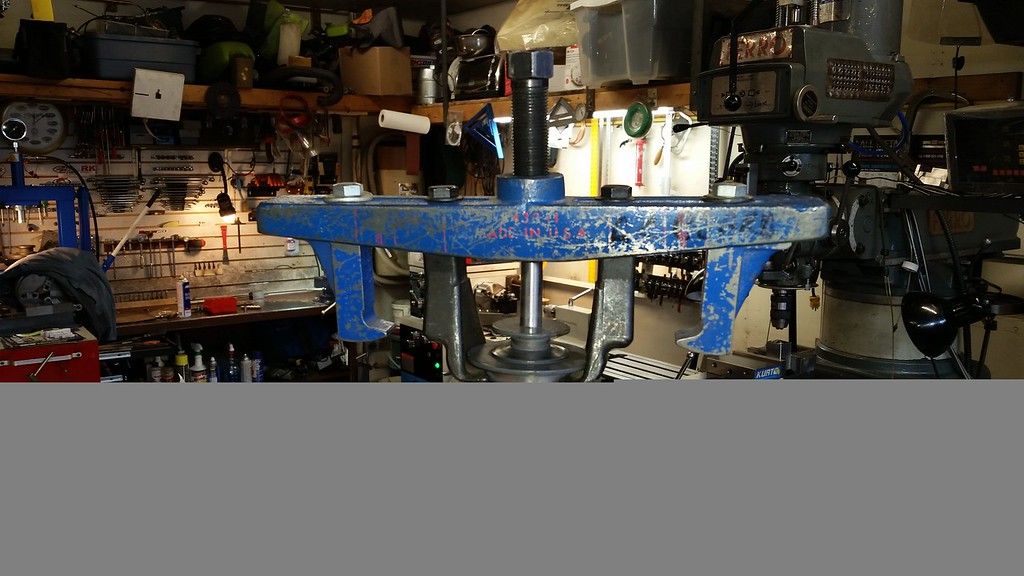
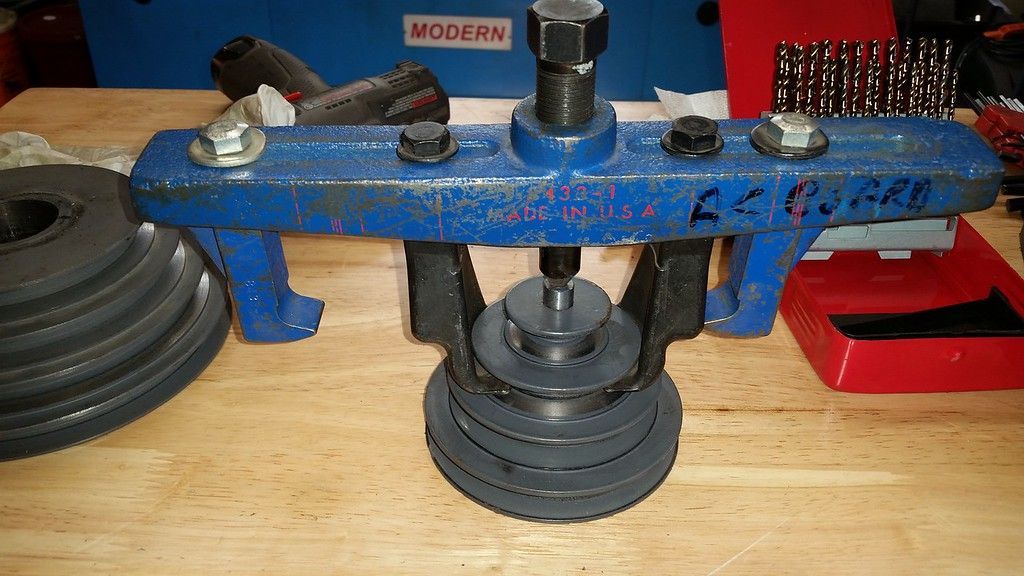
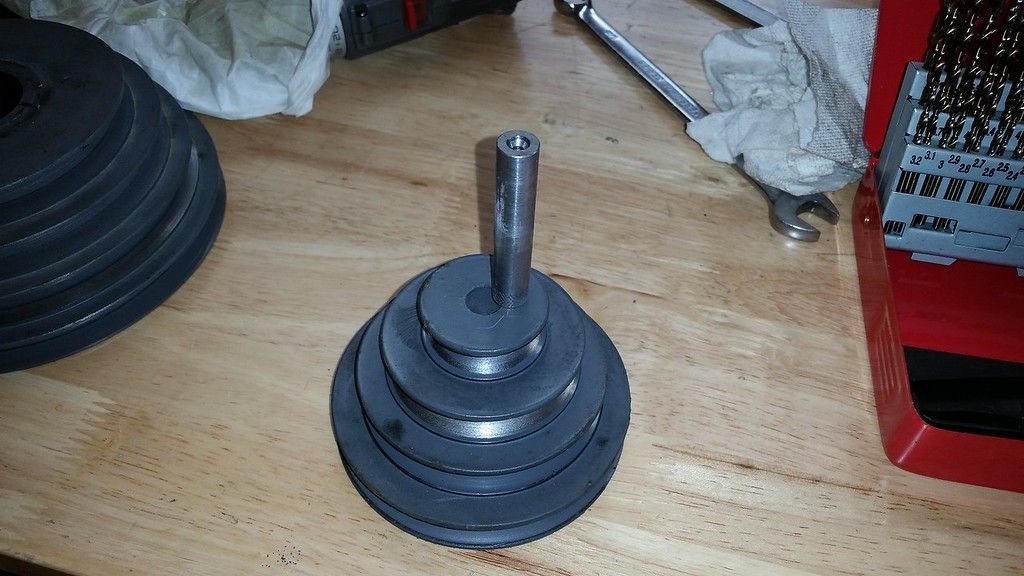
I mounted the tach magnet with epoxy to the bottom of the spindle pulley after milling a shallow pocket for it. I drilled a hole to mount the pick-up in the bottom of the belt shroud to align the pick-up with the magnet.
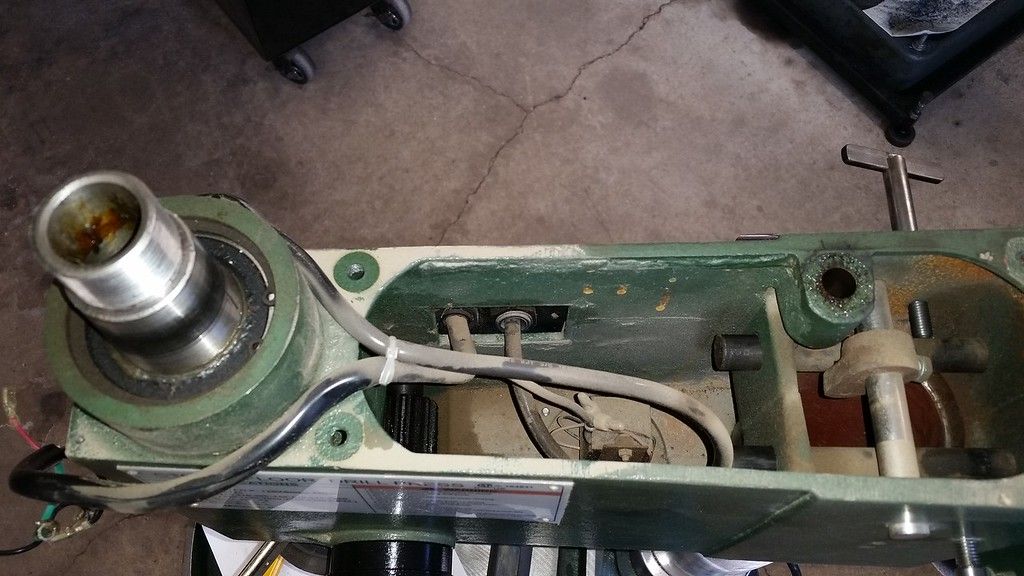
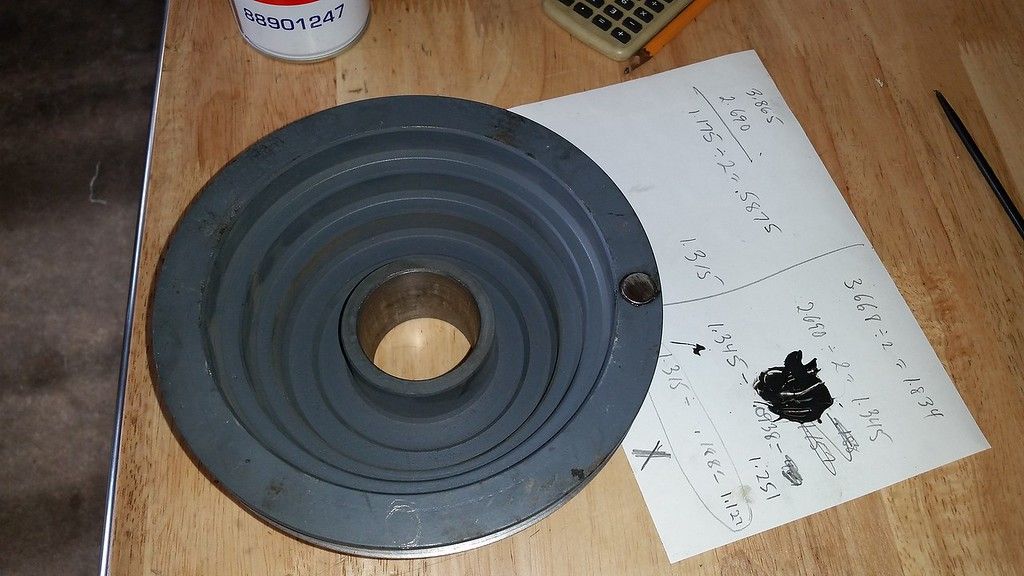
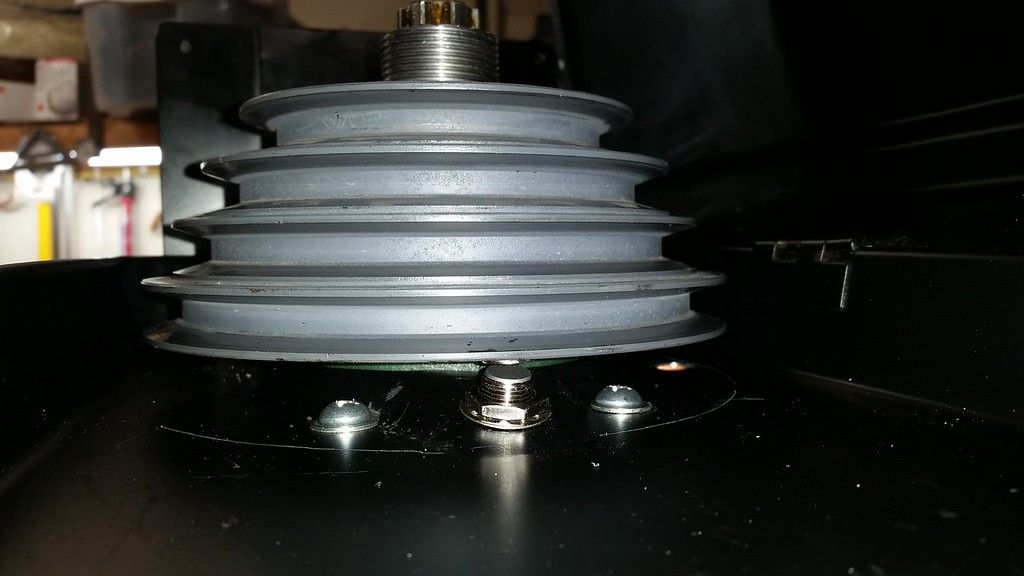
e.