Hoping folks can check my thinking.
The X axis ball screw that came in the kit I bought is too long for my table so I need to cut it down and machine the end.
I don't want to mess this up.
Here's some pics to illustrate the situation.
Here the excess length and the machined end.
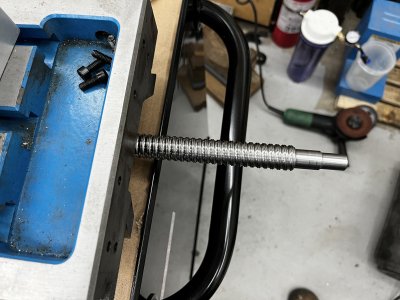
This is the bearing carrier and the mount that screws onto the end of the table.
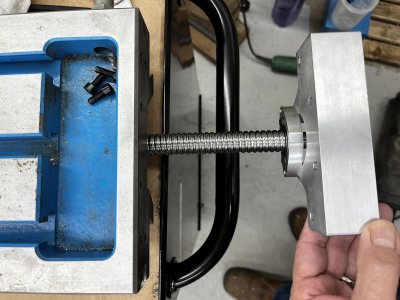
I measured the distance between the end of the table and the mount and came up with 130mm.
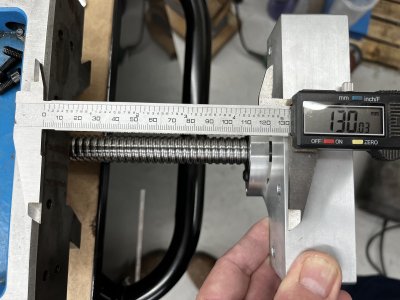
This is what 130mm looks like on the ball screw.
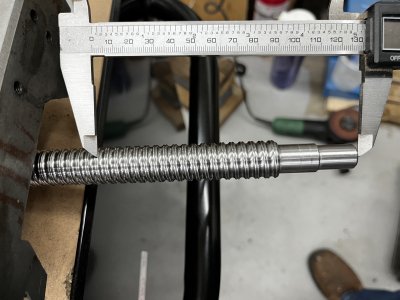
So my thinking is if I cut off 130mm of length then machine then machine the features on the end, the mount should bolt up to the table. For good measure I may make the bearing surface a smidge longer to make sure the mount seats well on the end of the table.
Is my thinking correct or am I overlooking something obvious?
The X axis ball screw that came in the kit I bought is too long for my table so I need to cut it down and machine the end.
I don't want to mess this up.
Here's some pics to illustrate the situation.
Here the excess length and the machined end.
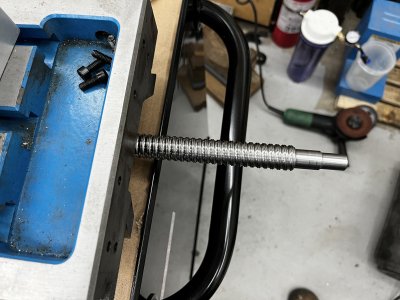
This is the bearing carrier and the mount that screws onto the end of the table.
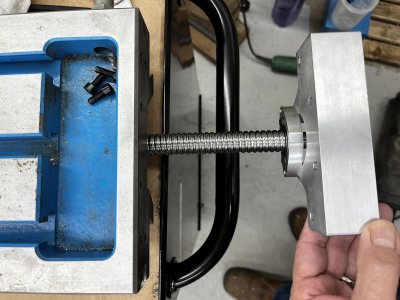
I measured the distance between the end of the table and the mount and came up with 130mm.
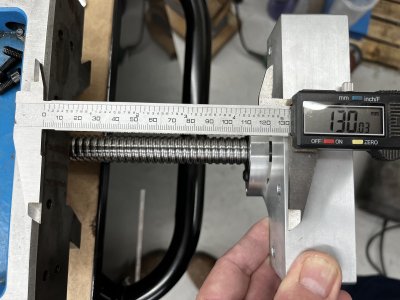
This is what 130mm looks like on the ball screw.
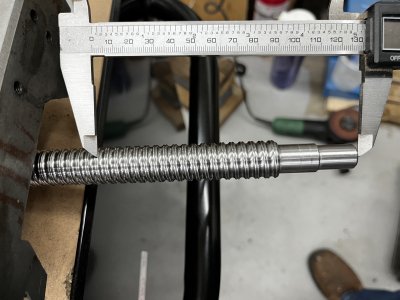
So my thinking is if I cut off 130mm of length then machine then machine the features on the end, the mount should bolt up to the table. For good measure I may make the bearing surface a smidge longer to make sure the mount seats well on the end of the table.
Is my thinking correct or am I overlooking something obvious?