I saw this video of a fly cutter build (did somebody post that here somewhere? thanks if you did) 3M views unbelievably. Interesting approach. In that video though his mill has 4 bolt holes parallel and part of the spindle that he can bolt the big disc too. I'm not sure what that kind of spindle is called. Here is the video
I was thinking about how to make one of these but something which would work with my equipment - an obvious but quite wasteful approach is to take a thick disc of material - say 3" thick and turn down a big portion of it to a small shaft that I could grab in a side lock tool older. e.g. quite similar to my face mill adapter I made recently: https://canadianhobbymetalworkers.com/threads/face-mill-adapter.3224/post-41804
Same kind of idea as Edge Precision making this huge part:
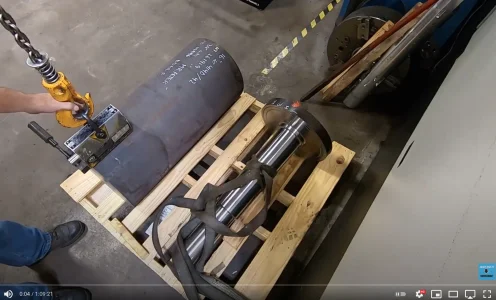
Simple and highly accurate approach - but that is a lot of material to turn into chips.
I was wondering about how else a disc could be attached to a shaft - tapers and key ways? Welding? Well no it would end up bent I'm sure. Well what about a press fit and drilled and threaded holes to replace a keyway? Is this a technique that could yield good results? Here is an example 1" hole with a 1.001" shaft - and interference press fit. Then holes drilled and threaded from the bottom 1/4-20 into the disc and shaft. Would the shaft end up 90 degrees to the disc? How big a press would one need to put the shaft into the disc? Would the screws even be necessary?
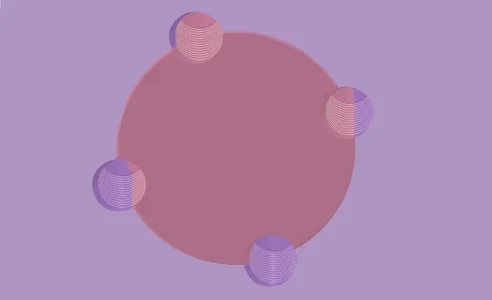
I was thinking about how to make one of these but something which would work with my equipment - an obvious but quite wasteful approach is to take a thick disc of material - say 3" thick and turn down a big portion of it to a small shaft that I could grab in a side lock tool older. e.g. quite similar to my face mill adapter I made recently: https://canadianhobbymetalworkers.com/threads/face-mill-adapter.3224/post-41804
Same kind of idea as Edge Precision making this huge part:
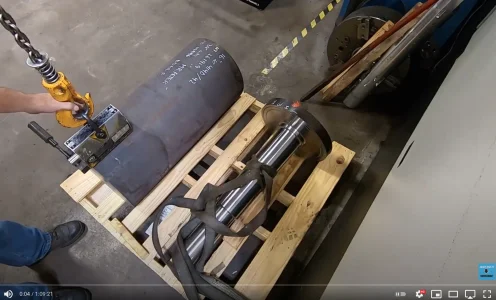
Simple and highly accurate approach - but that is a lot of material to turn into chips.
I was wondering about how else a disc could be attached to a shaft - tapers and key ways? Welding? Well no it would end up bent I'm sure. Well what about a press fit and drilled and threaded holes to replace a keyway? Is this a technique that could yield good results? Here is an example 1" hole with a 1.001" shaft - and interference press fit. Then holes drilled and threaded from the bottom 1/4-20 into the disc and shaft. Would the shaft end up 90 degrees to the disc? How big a press would one need to put the shaft into the disc? Would the screws even be necessary?
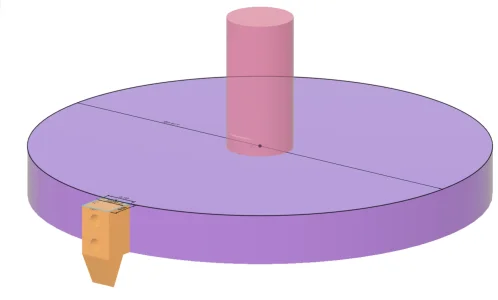
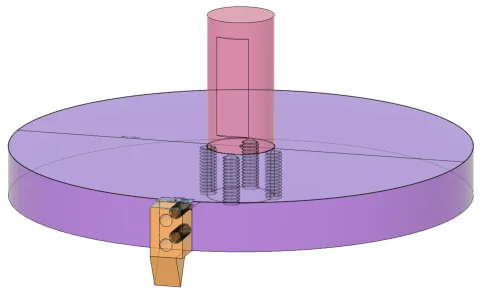
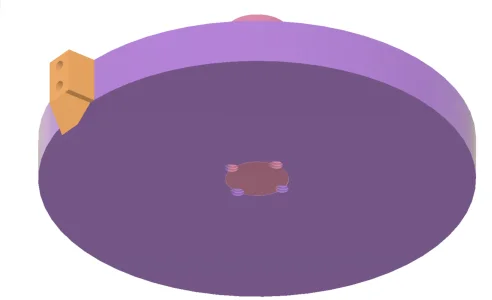
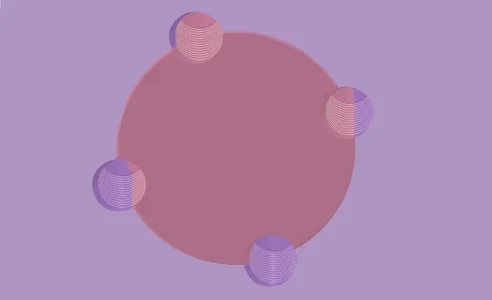
Last edited: