Bit of history first. The house is built into a hill so the front of the house is at ground level but it's really the basement. Stairs go up to the main level which is pretty well even with the ground level and the upstairs driveway. The basic foundation at the front is concrete about 8" wide or so. The framing for the front sits on this.
When we bought the house in 1997 we took out this old beat up shag carpet that was laying on the concrete and tossed it. The carpet on the main floor was pulled, the hardwood refinished and that carpet laid on the floor downstairs in what we called the family room.
A few years ago we replaced all the single pane aluminum framed windows (lots of ingots from that) with Pella Wood framed double and triple glazed. Downstairs in this family room it was roughed in after we pulled some of the wall paneling and there it has sat for the last 8 years or so.
The thin ugly wood paneling was spaced away from the framing to match the original aluminum frames. I can pull this now and add plastic vapor barrier and drywall. What I don't know is what to do with that concrete footing which sticks out from the wall. In fact the lifting the carpet shows lots of spider infestation over the decades and a layer of sand along the footing on top of the concrete floor.
So once I remove the spacers I'm thinking 3/4" foam board to wrap around the footing. For the floor those floating 2x2 foot panels with a vapor barrier under them too.
I'm thinking the wall vapor barrier goes over the foam and is connected to the floor vapor barrier.
So what order to do this?
1. Rip out all the wall panels to get access to the footing and lay down plastic and the floor panels.
1a. Or use the foam backed floor panels and forget about the plastic on the floor.
2. Put the foam panels over the footing.
3. Put on the wall vapor barrier and tape it to the floor plastic barrier that has been brought up.
Or is it better to lay the plastic on the floor and the foam on the footings and first tape the vapor barrier from wall to floor. Then put down the floor panels and cover the foam with plywood. Finally add the drywall?
When we bought the house in 1997 we took out this old beat up shag carpet that was laying on the concrete and tossed it. The carpet on the main floor was pulled, the hardwood refinished and that carpet laid on the floor downstairs in what we called the family room.
A few years ago we replaced all the single pane aluminum framed windows (lots of ingots from that) with Pella Wood framed double and triple glazed. Downstairs in this family room it was roughed in after we pulled some of the wall paneling and there it has sat for the last 8 years or so.
The thin ugly wood paneling was spaced away from the framing to match the original aluminum frames. I can pull this now and add plastic vapor barrier and drywall. What I don't know is what to do with that concrete footing which sticks out from the wall. In fact the lifting the carpet shows lots of spider infestation over the decades and a layer of sand along the footing on top of the concrete floor.
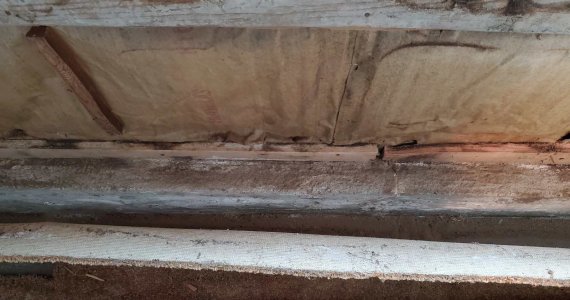
So once I remove the spacers I'm thinking 3/4" foam board to wrap around the footing. For the floor those floating 2x2 foot panels with a vapor barrier under them too.
I'm thinking the wall vapor barrier goes over the foam and is connected to the floor vapor barrier.
So what order to do this?
1. Rip out all the wall panels to get access to the footing and lay down plastic and the floor panels.
1a. Or use the foam backed floor panels and forget about the plastic on the floor.
2. Put the foam panels over the footing.
3. Put on the wall vapor barrier and tape it to the floor plastic barrier that has been brought up.
Or is it better to lay the plastic on the floor and the foam on the footings and first tape the vapor barrier from wall to floor. Then put down the floor panels and cover the foam with plywood. Finally add the drywall?
Last edited: