I spotted a YouTube where a guy repaired a broken bandsaw blade using silver solder. I have 2 broken blades, some SS, Flux, torch, and Map gas so I thought what the hey lets give it a go.
Clamp the blade ends together, apply flux and then silver solder. Probably a little to much SS there.
Grind off and smooth the excess with a Dremel.
Do the same for the other side.
This looked like it was actually going to work until the joint let loose while I was attempting to take a pic if it bent to about drive pulley radius.
Anyone else try or do this successfully? Do you think a spot welder would work for this kind of repair?
Craig
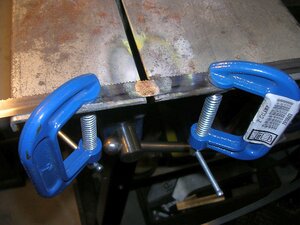
Clamp the blade ends together, apply flux and then silver solder. Probably a little to much SS there.
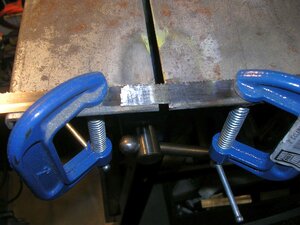
Grind off and smooth the excess with a Dremel.
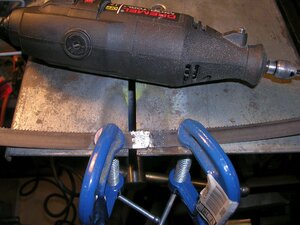
Do the same for the other side.
This looked like it was actually going to work until the joint let loose while I was attempting to take a pic if it bent to about drive pulley radius.
Anyone else try or do this successfully? Do you think a spot welder would work for this kind of repair?
Craig