slow-poke
Ultra Member
This question is related to this thread...
canadianhobbymetalworkers.com
I'm starting a new thread specific to the mounting block for the X axis for clarity.
This appears to be a typical engineering tradeoff scenario.
First a few image to help with the question:
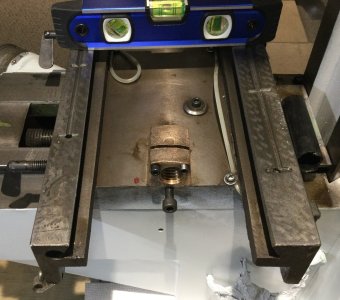
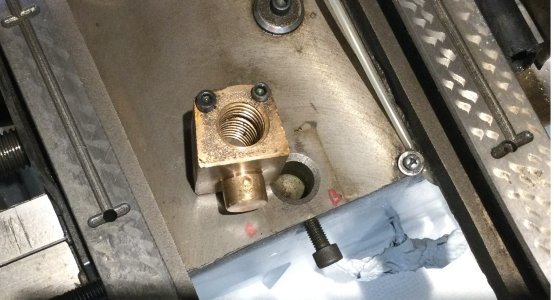
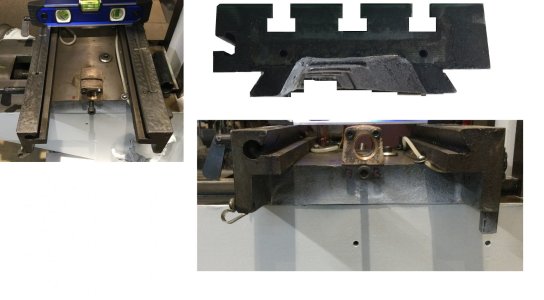
The original ACME screw is 22.12mm in diameter, 104.5mm long
The way the nut mounts is interesting, the round protrusion just slips in the hole of the saddle and then is locked in place with a hex cap socket style bolt. This must be by design probably so both the rotation and height of the nut can be tweaked for alignment and then snugged down. I did not pay much attention to this during disassembly, I just took the bolt out to free up as much as possible when taking the table off. I would imagine when assembling the nut will sort of self align if you spin the leadscrew and when it has found "home" you tighten up the bolt, does that make sense? Back to this later........
There appears to be two critical clearance areas, one above the nut and one below, the lower one being tighter.
The bronze nut is about 34.7mm tall, so on the bottom side the critical dimension is r =~17.3mm
Standard applicable ballscrew diameters are 16 and 20mm
16mm: https://www.ebay.ca/itm/266253645526
20mm: https://www.ebay.ca/itm/266256101855?hash=item3dfe19b1df:g:HlkAAOSwi49bKSFK
The circular shaped flange (with cutoff top and bottom) is the critical dimension; 40mm for the 16mm. and 44mm for the 20mm.
In both cases the easiest solution appears to be to let the flange hang over the edge of the saddle:
- with the 16mm ballscrew (40mm block height), quite likely I can reach the bolt if a slightly oval access hole is made in the mounting block.
- with the 20mm ballscrew (44mm block height), might still be possible, especially with the ball nose type hex key. The 36mm diameter of the round portion may also be a slight problem, because my rough measurement below the nut is 17.3mm so I might need to mill a slot at the low spot about 0.03" deep.
The other complication with the flange hanging over the side is that it prevents tweaking the angle (I suppose a shim could be placed between the new block and the front face to tweak if required)
Please post your thoughts.
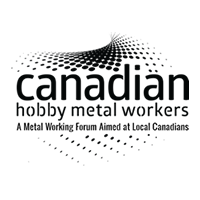
8x30 A1S mill Ball-screw upgrade?
Enquiring minds would like to know...... I took a look at the X axis lead screw on my partially disassembled mill and I think it looks okay (it certainly felt great), except where the power drive meshed with it, in that location it looks terrible. I have no plan to use the power drive because I...
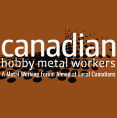
I'm starting a new thread specific to the mounting block for the X axis for clarity.
This appears to be a typical engineering tradeoff scenario.
First a few image to help with the question:
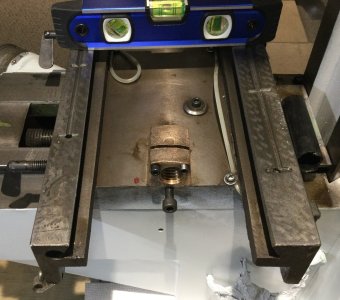
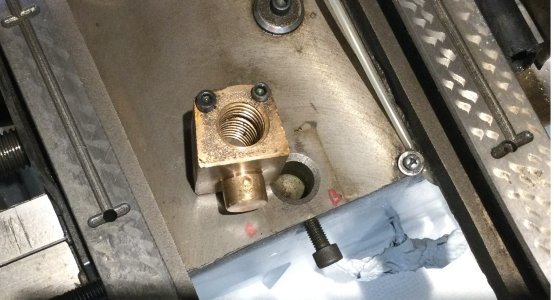
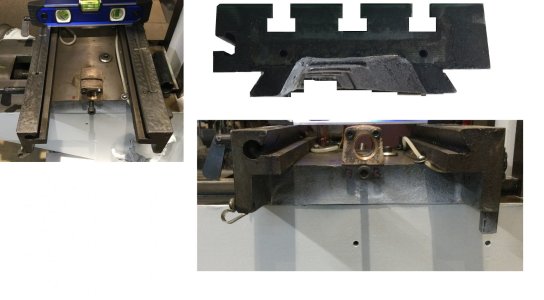
The original ACME screw is 22.12mm in diameter, 104.5mm long
The way the nut mounts is interesting, the round protrusion just slips in the hole of the saddle and then is locked in place with a hex cap socket style bolt. This must be by design probably so both the rotation and height of the nut can be tweaked for alignment and then snugged down. I did not pay much attention to this during disassembly, I just took the bolt out to free up as much as possible when taking the table off. I would imagine when assembling the nut will sort of self align if you spin the leadscrew and when it has found "home" you tighten up the bolt, does that make sense? Back to this later........
There appears to be two critical clearance areas, one above the nut and one below, the lower one being tighter.
The bronze nut is about 34.7mm tall, so on the bottom side the critical dimension is r =~17.3mm
Standard applicable ballscrew diameters are 16 and 20mm
16mm: https://www.ebay.ca/itm/266253645526
20mm: https://www.ebay.ca/itm/266256101855?hash=item3dfe19b1df:g:HlkAAOSwi49bKSFK
The circular shaped flange (with cutoff top and bottom) is the critical dimension; 40mm for the 16mm. and 44mm for the 20mm.
In both cases the easiest solution appears to be to let the flange hang over the edge of the saddle:
- with the 16mm ballscrew (40mm block height), quite likely I can reach the bolt if a slightly oval access hole is made in the mounting block.
- with the 20mm ballscrew (44mm block height), might still be possible, especially with the ball nose type hex key. The 36mm diameter of the round portion may also be a slight problem, because my rough measurement below the nut is 17.3mm so I might need to mill a slot at the low spot about 0.03" deep.
The other complication with the flange hanging over the side is that it prevents tweaking the angle (I suppose a shim could be placed between the new block and the front face to tweak if required)
Please post your thoughts.