Here’s an old motor that is now a buffer/polisher. Threaded rod was welded to the splined shaft to secure a buffer disc or wire wheel.
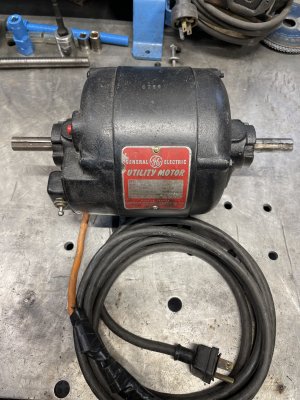
In pic below, the threaded rod extension is clamped on and aligned by using a piece of angle:
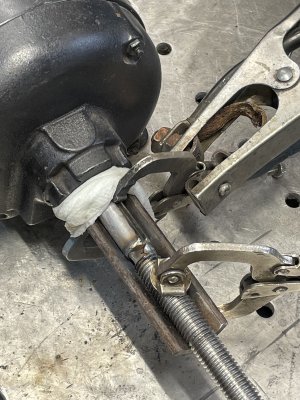
The indicator is set up on a bushing to check runout. A weight was hung from the bushing set screw threaded hole so that the bushing did not rotate with the shaft.
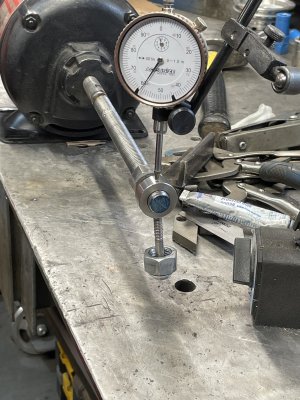
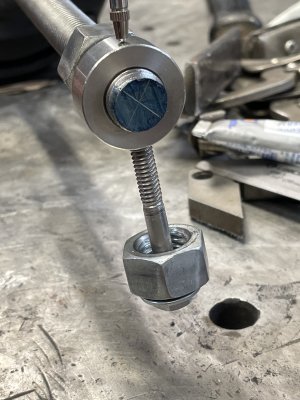
Weld access was improved by using bushings as spacers:
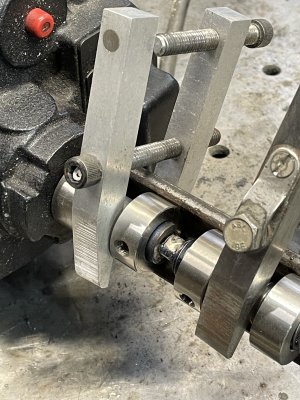
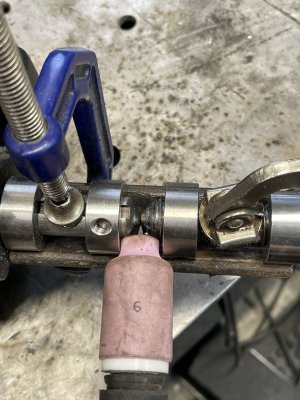
After welding, shaft runout was 0.035” at the end of the 8” long threaded rod extension. (Note: The extension was to be 1.75 inches. It was cut to length later.) Straightening the shaft extension was done by cutting a V notch and re-welding. Then the shrinkage during cooling pulled it into better alignment. (Using a hydraulic press to straighten the shaft didn’t seem like a good option.)
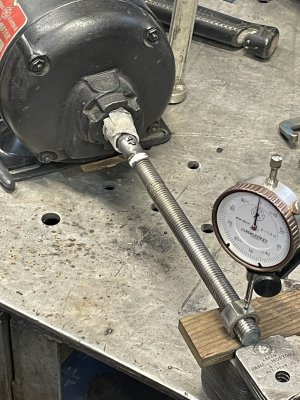
and a close up of the V notch:
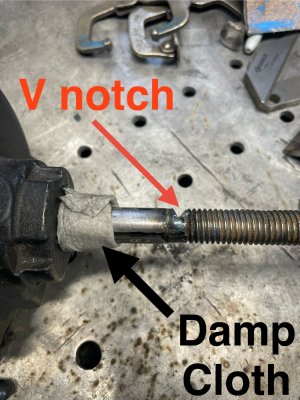
It was a bit of trial and error to determine the size of the notch. After a few attempts, runout was reduced to 0.008 inches at 8 inches. Likely runout could be reduced to 0.005” or less, but that seemed unnecessary. It was easy to overshoot the target and have the runout switch from negative to positive instead of getting closer to zero.
It was finished last week. It runs very smoothly after balancing the 10” wire wheel and buffer discs. Now it needs a stand and to be bolted down.
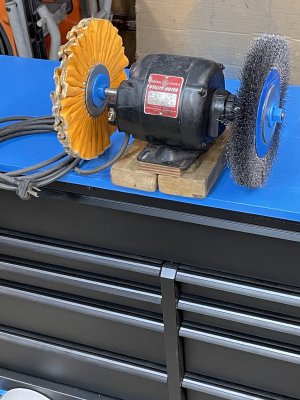
PS. There is enough thread to use a second nut as a lock-nut (on the left side instead of left-hand threaded rod). Using a deformed locking nut (instead of a pair of nuts) worked well too.
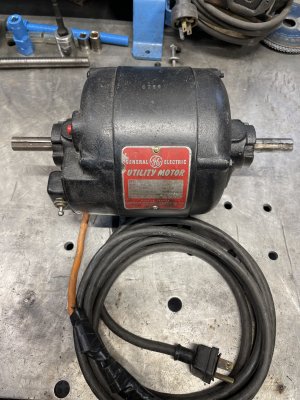
In pic below, the threaded rod extension is clamped on and aligned by using a piece of angle:
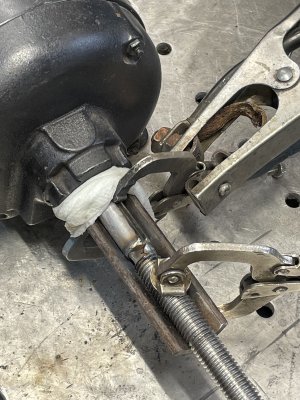
The indicator is set up on a bushing to check runout. A weight was hung from the bushing set screw threaded hole so that the bushing did not rotate with the shaft.
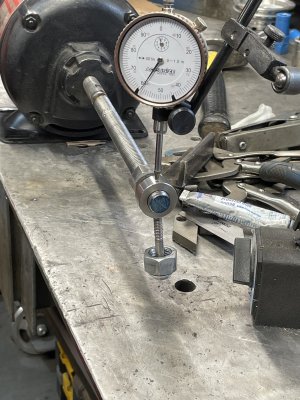
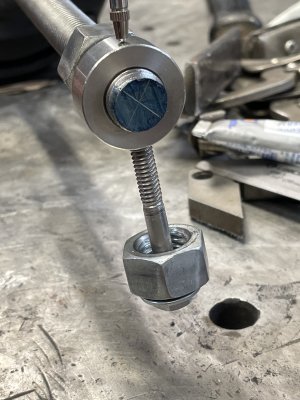
Weld access was improved by using bushings as spacers:
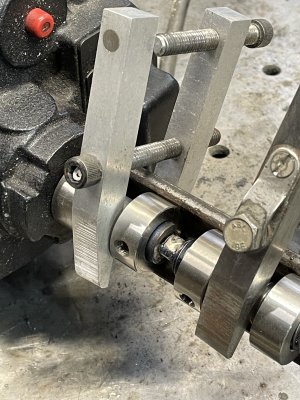
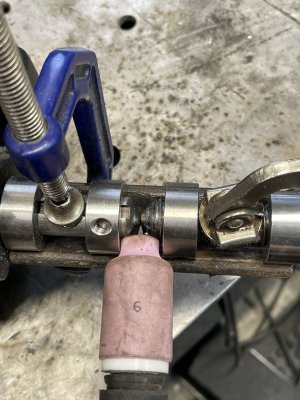
After welding, shaft runout was 0.035” at the end of the 8” long threaded rod extension. (Note: The extension was to be 1.75 inches. It was cut to length later.) Straightening the shaft extension was done by cutting a V notch and re-welding. Then the shrinkage during cooling pulled it into better alignment. (Using a hydraulic press to straighten the shaft didn’t seem like a good option.)
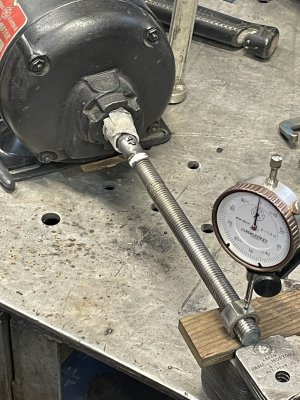
and a close up of the V notch:
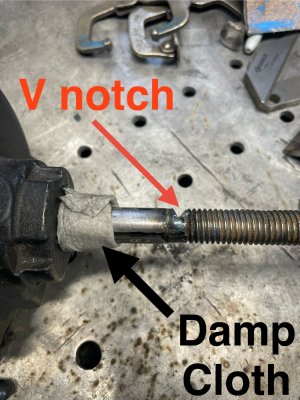
It was a bit of trial and error to determine the size of the notch. After a few attempts, runout was reduced to 0.008 inches at 8 inches. Likely runout could be reduced to 0.005” or less, but that seemed unnecessary. It was easy to overshoot the target and have the runout switch from negative to positive instead of getting closer to zero.
It was finished last week. It runs very smoothly after balancing the 10” wire wheel and buffer discs. Now it needs a stand and to be bolted down.
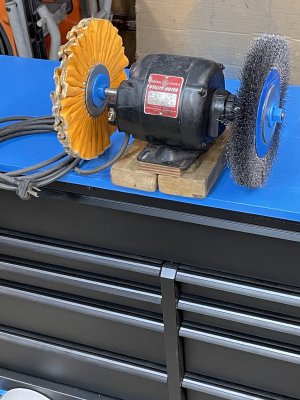
PS. There is enough thread to use a second nut as a lock-nut (on the left side instead of left-hand threaded rod). Using a deformed locking nut (instead of a pair of nuts) worked well too.