I'm too lazy to go hunting but seems like someone on the forum mentioned they have the (likely Shars) 5C collet based D-bit grinder. Who be you?
www.shars.com
I'm interested to confirm the dimensions of the dovetail on work head & flute attachment, which should be the same.
Also, I assume the threads of tightening arbor on the work head engage the inner 5C collet threads?
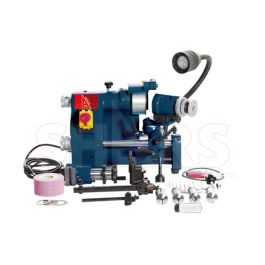
Universal End Mill Cutter Drill Bit Grinder Sharpener
I'm interested to confirm the dimensions of the dovetail on work head & flute attachment, which should be the same.
Also, I assume the threads of tightening arbor on the work head engage the inner 5C collet threads?