Working on a project to add secondary plugs to vw cylinder heads, im trying to figure out the best way to cut through the cooling fins in order to make a spark plug seating surface, and clearance for the plug socket. The simplest way i have been able to figure is the biggest endmill i can run, 22mm, plunge through the path of the drill bit to make the seat, and clearance all in 1.
Question is, 2 or 4 flute endmill ? i know the normal answer is 2 for aluminum, but im wondering if thats the best choice here, given the size of endmill there is lots of room for chips, and the interrupted cut through the fins might be problematic with 2 flutes. Thoughts ?
I have found 22mm in 2 and 4 flute for 26$ ea (HSS), i could buy both, but i would rather not, what the heck am i going to use a 22mm hss endmill for beyond this
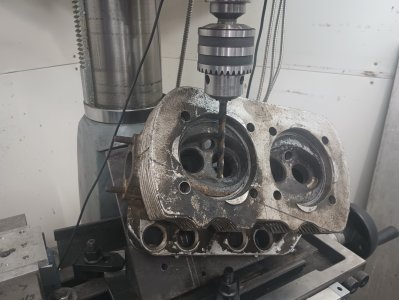
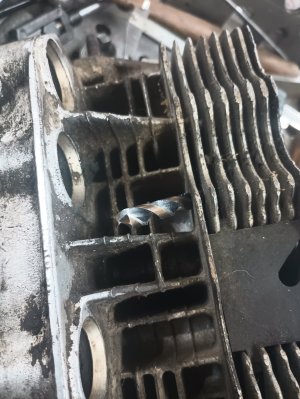
Question is, 2 or 4 flute endmill ? i know the normal answer is 2 for aluminum, but im wondering if thats the best choice here, given the size of endmill there is lots of room for chips, and the interrupted cut through the fins might be problematic with 2 flutes. Thoughts ?
I have found 22mm in 2 and 4 flute for 26$ ea (HSS), i could buy both, but i would rather not, what the heck am i going to use a 22mm hss endmill for beyond this
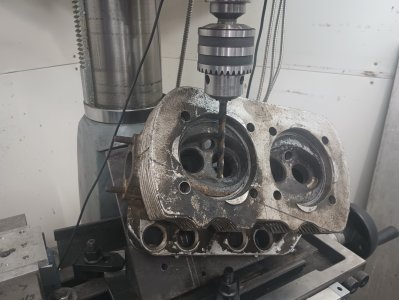
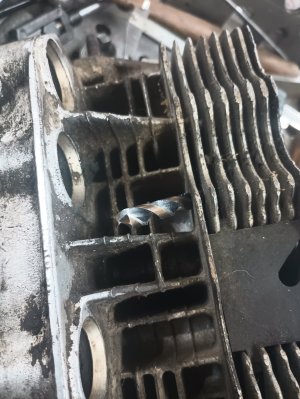