So, I've been commissioned by my daughter to make another one of these.......
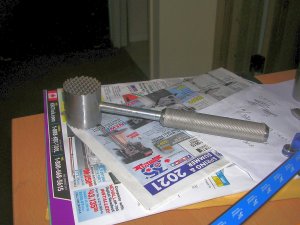
Ya, Ya, I know... grade 9 shop stuff. I made this one about 5 years ago on my mini-mill and utilathe. Will make a good excuse to fire up the shaper.
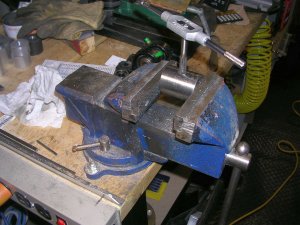
Tapping the head 3/8-16.
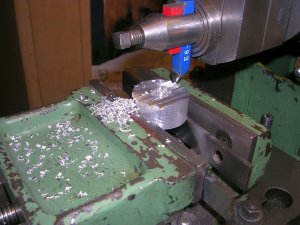
Here I'm experimenting on some aluminum to determine what a suitable down feed and side step would be. Looks like 0.1" down and a 0.15" side step will work nicely.
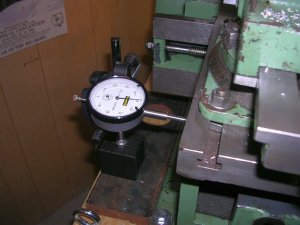
My shaper has a ridiculously small dial for indicating table travel. And no witness mark to align it with
So I'm using my dial indicator to measure side step.
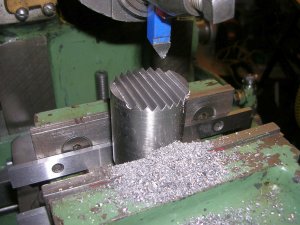
One face of the head done. That there probably amounted to 2 hours of standing at the shaper down feeding. Not the quickest machining operation that's for sure.
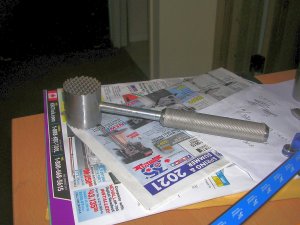
Ya, Ya, I know... grade 9 shop stuff. I made this one about 5 years ago on my mini-mill and utilathe. Will make a good excuse to fire up the shaper.
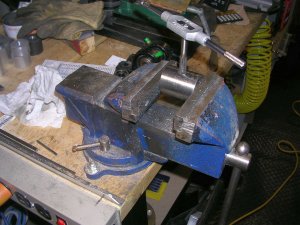
Tapping the head 3/8-16.
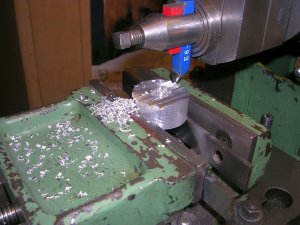
Here I'm experimenting on some aluminum to determine what a suitable down feed and side step would be. Looks like 0.1" down and a 0.15" side step will work nicely.
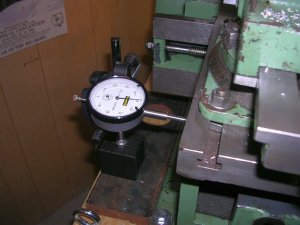
My shaper has a ridiculously small dial for indicating table travel. And no witness mark to align it with

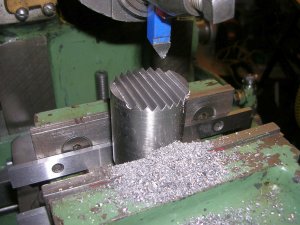
One face of the head done. That there probably amounted to 2 hours of standing at the shaper down feeding. Not the quickest machining operation that's for sure.