Used my new to me cnc mill today on its longest and most nerve wracking project to date. I made a fixture plate with reamed holes and threaded holes in an offset pattern.
65 holes total, 33 tapped and 32 reamed.
3/4" spacing cause that looked nice and I'm planning on using this on small parts. Overall its a bit under 4" wide by 10" long as that was the size of salvaged plate I had. Only broke one tap on a setup piece as I was learning the settings for the tension compression tapping head.
Used the surface grinder cause I have one, and it gave a nice surface finish.
Next is to make some clamps to go with it. Not sure when that will happen. Need to get some ideas for those, maybe copy the Joe Pie ones.
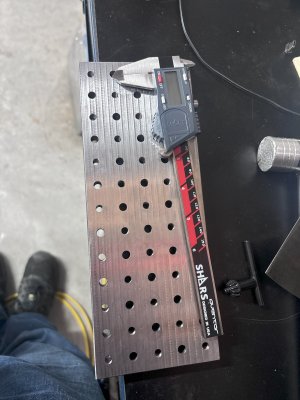
65 holes total, 33 tapped and 32 reamed.
3/4" spacing cause that looked nice and I'm planning on using this on small parts. Overall its a bit under 4" wide by 10" long as that was the size of salvaged plate I had. Only broke one tap on a setup piece as I was learning the settings for the tension compression tapping head.
Used the surface grinder cause I have one, and it gave a nice surface finish.
Next is to make some clamps to go with it. Not sure when that will happen. Need to get some ideas for those, maybe copy the Joe Pie ones.
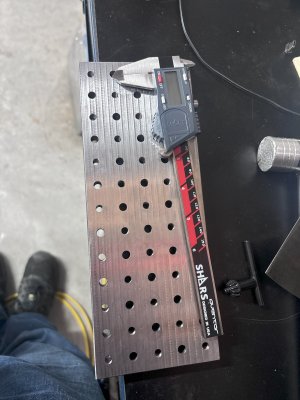