So I have one of those Uber cheap 30" sheet metal brakes from princess auto and I was attempting some fixes to some of the well know weaknesses in the unit.
The bending angle is known to flex in the middle especially on full width bends or on heavier gauge stuff. I've seen various videos where other people welded on reinforcing steel on the back side to prevent this. I thought many of them were overkill and was worried that alot of welding would warp the angle. That's exactly what I ended up with, a warped bending angle that has now turned my brake into scrap as it now sits.
I figured 3 flat bar gussets in the angle would be adequate strength but didn't think warpage would be of concern. I was wrong.
The only thing I can think of that MIGHT help is to cut through the middle gusset and hope that might relieve some of the strain. Grinding the surfaces flat again isn't really an option as the angle binds now and there is no way I can see that the angle can be removed.
Suggestions?
The bending angle is known to flex in the middle especially on full width bends or on heavier gauge stuff. I've seen various videos where other people welded on reinforcing steel on the back side to prevent this. I thought many of them were overkill and was worried that alot of welding would warp the angle. That's exactly what I ended up with, a warped bending angle that has now turned my brake into scrap as it now sits.
I figured 3 flat bar gussets in the angle would be adequate strength but didn't think warpage would be of concern. I was wrong.
The only thing I can think of that MIGHT help is to cut through the middle gusset and hope that might relieve some of the strain. Grinding the surfaces flat again isn't really an option as the angle binds now and there is no way I can see that the angle can be removed.
Suggestions?
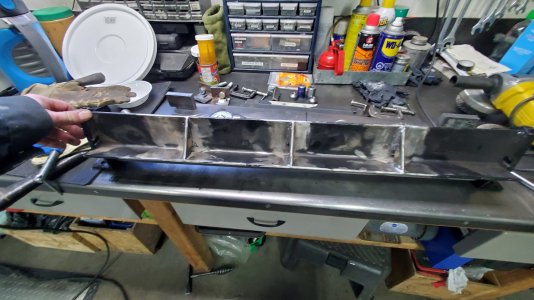
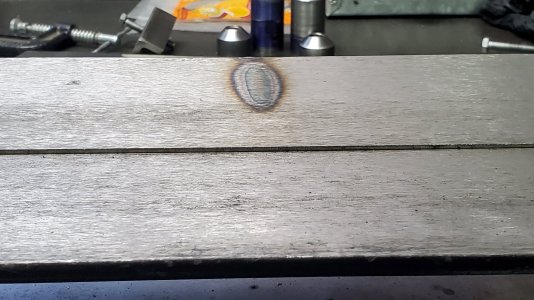