Was talking to a coworker today, and noticed a nice little die grinder in the top of his toolbox. Had a closer look, and realized it’s a Dotco! Someone gave it to him for free, but… the end cap’s missing.
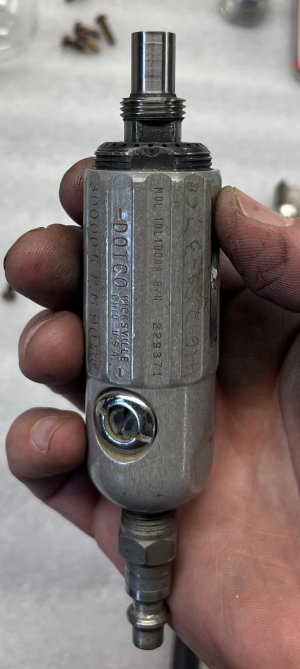
The male thread at the front appears to be 1 1/8”-18 UNEF. Trying to decide if I have a practical way to make a cap for it.
I have an internal threading insert holder I picked up a few years ago, maybe time to dig into Stel’s excellent presentation on threading from the Ontario meetup?
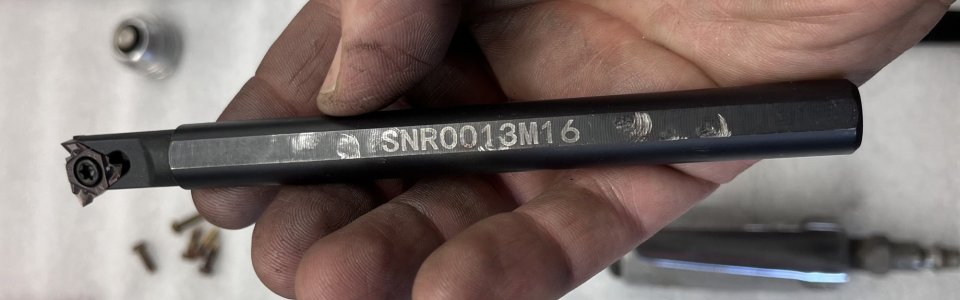
A little tricky, in that its internal, threading up to (more likely away from…) a shoulder, over a fairly short length of thread (~1/4”), and the cap can’t be too tall (less than 5/16”) or it’ll block the wrench flats for tightening the collet.
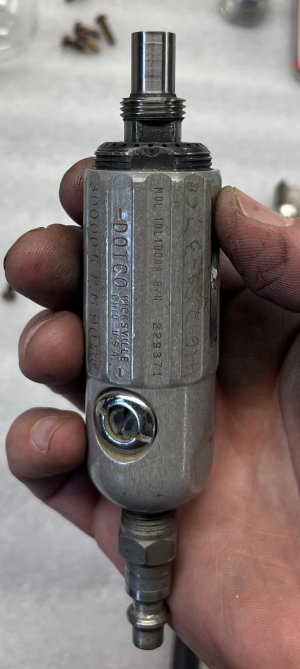
The male thread at the front appears to be 1 1/8”-18 UNEF. Trying to decide if I have a practical way to make a cap for it.
I have an internal threading insert holder I picked up a few years ago, maybe time to dig into Stel’s excellent presentation on threading from the Ontario meetup?
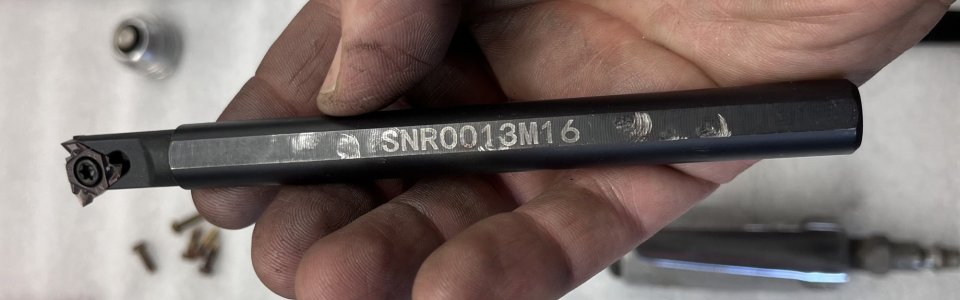
A little tricky, in that its internal, threading up to (more likely away from…) a shoulder, over a fairly short length of thread (~1/4”), and the cap can’t be too tall (less than 5/16”) or it’ll block the wrench flats for tightening the collet.